EPOXY RESINS
- Casting resins – clear, low-viscosity epoxies for production of epoxy cast tables, doors, headboards, clocks, lamps, jewelry, serving boards, etc.
- Special (effects) resins – developed for special purposes (such as painting and geode art, repeated thin layer casting, high-strength deformed wood repairs, fast, quick product repairs etc.).
- Penetration resins – to seal porous materials (wood) and thus eliminate bubbles when curing the casting resin. Also to create an adhesive bridge for the next layers.
- Coating, table top resin – for top coat casting or overlaying of wooden surfaces (tables, coffee tables, clocks, etc.).
- Stabilizing resins – for strengthening and stabilizing rotten or unpaved parts of wood, and for making stabilized wood for luxury products (knife handles, jewelry, golf club handles, luxury car levers, luxury pens, etc.).
- Floor resins – casting resins for design cast floors and 3D clear floors.
- Laminating Resins – lower viscosity two-component epoxy systems for laminating composite materials, whether by manual lamination, winding, RTM/RIM/SCRIMP or infusion.
- Food certification – Important if you make tables, tables, bowls, etc., products that come in contact with food.
- UV resistance – Defines the UV resistance of the resin. UV radiation causes degradation = yellowing of each epoxide and this parameter tells us how long and to what shade the resin changes shade. There are epoxies yellowing to a deep yellow color in a few months to epoxies changing their color to a very soft yellowish color in 5-6 years on the market.
- Gelation time – Defines the time it takes for the resin to polymerize enough to increase its density to a honey consistency. Most pigment effects are formed at this time.
- Mixing ratio – This is the calculated ratio of resin (component A) to hardener (component B) that needs to be adhered to as much as possible and the resin should have the correct properties.
- Workability time – The time it takes to work comfortably with the resin.
- Full cure time – The time after which the resin is already cured, the epoxy is fully polymerized and is ready to be machined by grinding, milling, polishing, drilling, turning, etc.
- ShA hardness – Determines how hard or tough the material is after curing, evaluated with SHORE method. The ideal value is between 75-80ShA. Too hard systems are then more fragile and at the same time unable to absorb the internal stresses caused by wood working.
- Maximum casting layer – Maximum layer which can be cast at one time without the risk of an exothermic reaction ("boiling" of the resin).
- Maximum casting volume – Maximum volume of resin that can be mixed and cast at one time without the risk of an exothermic resin reaction ("boiling").
- Glass transition temperature – Determines the temperature resistance of the epoxy. This is the temperature at which the polymer changes from a hard glassy state to a flexible rubbery state. The process is reversible, ie when the temperature is reduced, the polymer hardens again.
- Epoxy shrinkage – Defines the epoxy volume loss during curing. It is manifested by a decrease in the casting level during curing and micro-waves on the surface of the cured casting.
- Epoxy viscosity in mPa.s – Shows how fluid the resin is. Casting resins tend to have lower viscosity, while resins for various effects have higher viscosity.
-
Casting resins for small castings – Such as jewelry, pens, small decorations, coasters, etc. This type of resin tends to be thin, fast to cure (on the order of hours up to 1 day), clear, harder and more fragile.
-
Casting resins for medium castings – Such as epoxy serving boards, small pieces of furniture, epoxy lamps, epoxy clocks, medium coffee tables made of epoxy resin and wood, etc. This type of resin tends to be thin, slower in curing (2-3 days), however, layers up to eg. 5 cm can be cast with them, they are usually clear, hard.
-
Casting resins for large castings – Such as resin and wood dining tables called river tables, coffee tables, doors, headboards, epoxy vases, larger pieces of furniture, etc. These epoxy resins tend to be sparse, slow to cure (3-5 days), they can cast larger volumes (up to eg. 50 L), and higher layers (eg. 10-12 cm).
-
Table top resin – For creating of a "glass" surface on wood and resin castings. This type of clear resin is thin, relatively fast to cure, with good flow, minimal shrinkage and good surface resistance.
-
Artistic casting resins – For creating epoxy images, geode art, various effects, etc. Resins of this type are thick, relatively fast to cure, clear, with minimal shrinkage.
-
CLEAR CASTING RESINS
-
WOOD STABILIZATION RESINS
-
SPECIAL RESINS
-
LAMINATION RESINS
-
WOOD PENETRATION
-
FLOOR RESINS
Bestsellers
Brands
Certifikace styku s potravinami
DLE TYPU PRYSKYŘICE
MAX. VRSTVA LITÍ
TYP VÝROBKU
UV stabilita

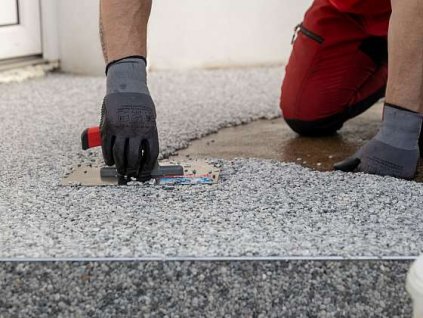
CHS EPODUR STONE UV is an epoxy resin with higher resistance to UV radiation for stone carpets, for the revitalization and restoration of old surfaces and for extending the life of concrete structures. Packaging: set of resin and hardener 14.3 kg.
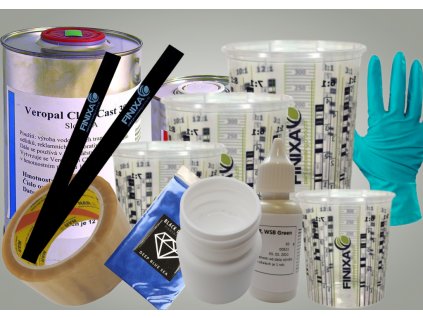
A package for beginners. Resin and necessary accessories for the first casting and getting basic knowledge about epoxy resin.
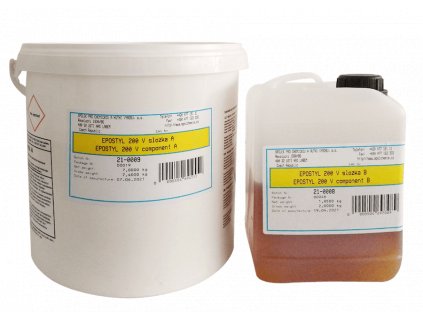
EPOSTYL 200V is a two-component transparent epoxy resin used as a penetrating coating for concrete or as a final surface varnish for wood, e.g. as a transparent coating for parquet floors in gymnasiums and living rooms. Packaging: 8.85 kg (7 kg component A + 1.85 kg component B)