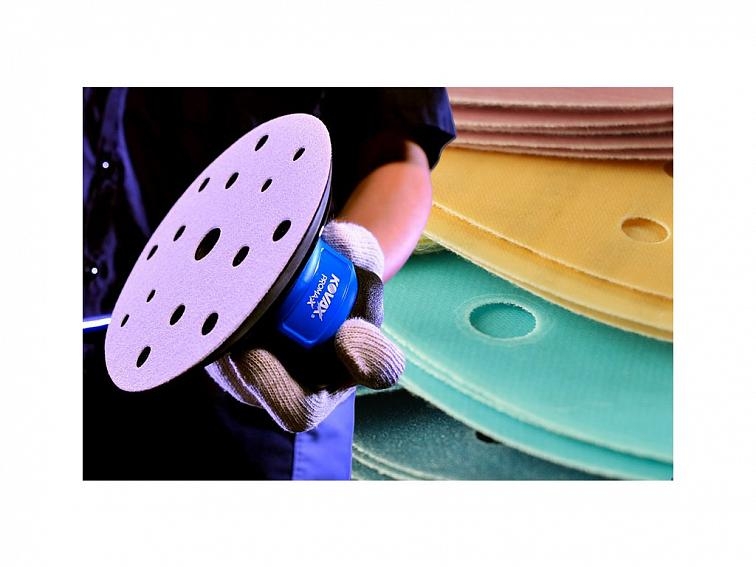
Kinds of sanding
- 1. Manual sanding
- 1A. Larger surfaces
- 1B. Manual sanding of trifles
- 1C. Manual sanding of articulated objects
- 2. Machine sanding 150 mm
- 3. Machine sanding 125 mm
- 4. Manual polishing
- 5. Machine polishing
General principles for sanding
- In general, we recommend starting sanding epoxy surfaces ideally 14 or more days after casting, but at least 10 days. The reason is the fact that the casting must be hardened as much as possible. The more hardened it is, the better sandable it is, the consumption of abrasive is lower and the length of sanding is significantly shorter. By sanding an unhardened casting, we will never sand the casting perfectly.
- Some grits are not skipped, they are always sanded from the roughest to the finest.
- The uniformity of the sanded surface is checked in the light, and the next roughness is only taken when the surface is pretty uniform. Each deeper mark is sandable very poorly and long time with a higher grain size.
- For a mirror shine, sand to 3000 grit and then polish with Finix paste on an orange foam pad. For a matt look, we can go anywhere from K240 depending on when we like the degree of matt on the epoxy.
- During sanding, the surface of the abrasive and the surface of the sanded surface are wiped with a microfibre cloth. If the sander does not have suction, it is necessary to clean both surfaces more often during sanding.
- No pressure is applied to the abrasive during sanding (pressure on the abrasive may cause scratches, which may appear only after the final polishing – then it is necessary to return to the grain size to sand out the scratch).
- During sanding, don't forget to protect your eyes and respiratory tract!
1. Manual sanding of surfaces
After flattening the plane of the casting on a milling machine, CNC, in a draft or on a leveling sander, we will have a semi-finished product ready for sanding. The marks on the surface of the casting after such straightening should ideally be fine-tuned to a plane with sandpaper with a grit of approx. P80. We can then use manual sanding to finish the product into its final form. However, we recommend using it only for smaller products.
For manual sanding of epoxy surfaces, we recommend using sanding formats of sanding papers with suitable grits.
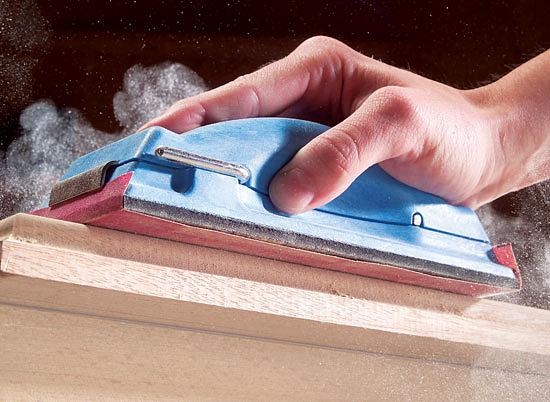
1A. Larger areas
For manual sanding of the Super Assilex abrasive formats, use the Super Assilex manual block with intermediate layer 9710094 for grits K240, K320, K360, K400 and K600. For finer sanding with grits K800, K1000, K1200 and K1500, use the soft intermediate layer 9710025. For fine sanding with the abrasive formats Buflex Dry K2000, K2500 and K3000, then use the soft velor Kovax Buflex Dry intermediate layer 9710060. During sanding, wipe the surface of the abrasive and the surface ground surfaces. Do not press on the abrasive when sanding.
1B. Manual sanding of details and trifles
A small format self-adhesive Tolecut sandpaper is used on a Toleblock sanding pad. It is mainly applied to the sanding of details on tables with broken wood (e.g. eyewood with epoxy), as well as to rings, earrings, bracelets, but also to mistakes in the paint, etc. We will use the self-adhesive Toleblock abrasive on the Toleblock stone. P800, P1200, P1500, P2000, P2500, P3000 grits are available. A different coarseness of the abrasive is stuck on each side of the Toleblock (it is easier to eventually return to the previous grit) and we sand when dry and wipe the dust with a cloth both from the casting and from the sanding block. It is important not to push, not to hurry and not to skip individual grits.
1C. Manual sanding of surfaces, radii, and differently articulated and shaped castings
For the processing of round surfaces, radii, and differently shaped castings, it is necessary to use the Super Assilex 9710025 soft pad. The abrasive format is simply attached to it directly using the integrated micro velcro. When sanding, we proceed from the roughest Super Assilex K240 abrasive formats, then 320, 360, 400, 600, 800, 1000, 1200 up to K1500 by individual roughness. For very soft sanding with Buflex Dry abrasive with grits of 2000, 2500 and 3000, we use the Kovax Buflex Dry intermediate layer pad 9710060, where the abrasive is attached to the soft side using a microzip.
2. Machine sanding - 150 mm
We recommend starting to sand epoxy surfaces ideally 14 or more days after casting, but at least 10 days. After flattening the plane of the casting on a milling machine, CNC, in a draft or on a leveling sander, we will have a semi-finished product ready for sanding. The marks on the surface of the casting after such flattening should ideally be fine-tuned to a plane with Tri-Pro P80 sandpaper. For hard sanding of an epoxy table or serving board, a wide-belt sander (if we have access to it) or, in most cases, an eccentric sander with oscillating motion and oscillation can be used 5 mm. A five millimeter offset in conjunction with Kovax abrasive is better, faster, more efficient and with a better result than a 3mm offset. We recommend not using a vibrating sander, which only vibrates in one direction, it clogs the abrasive a lot, it does not sand the epoxy as it should, and the choice of abrasive for this sander is also limited. We also do not recommend sanding with a drill or angle grinder, as the rotational movement results in poorer surface quality (ripples).
For efficient use of the abrasive and a perfect result when working with Kovax abrasive, we set the sanding speed on the eccentric sander to about half of the speed spectrum (mostly it is the 3rd level out of 6). This will reduce the speed, removal and heating of the material (epoxy does not like high temperatures). Above all, do not put pressure on the sander (a lot of pressure on the sander will cause scratches that will appear, for example, only after the final polishing – then it would be necessary to go back with the grain size and start the entire sanding almost from the beginning - for example, from grit 240). Hold the sander in the place where the axis passes through it – care must be taken that the sander does not lift up on one side or vice versa and thus create undulation errors by sanding. It is necessary to grind evenly over the entire surface.
Working procedure:
Start with the roughness of the abrasive with which you have prepared the product – sanded (e.g.: if the product is sanded with a wide belt sander to a grain size of 120, we first sand with abrasive grit 120).
If you start sanding with Kovax Tri-Pro abrasive, sand without an intermediate layer in the order of roughness 80, 100, 120, 150, 180, 220. During sanding, wipe the surface of the product and the surface of the abrasive with a cloth. Always check that the abrasive is sharp enough. If you continue the economical way further with Tri-Pro 240, 280, 320, 360, 400, 500, 600 abrasives, again do not use any intermediate layer. If you want to sand faster, more precisely and more evenly, use the higher quality Kovax Super Assilex 240, 320, 360, 400, 600 abrasive with a hard Super Assilex interlayer 9710057. The interlayers are necessary so that the hooks on the sander do not pierce the very elastic abrasive on latex and did not scratch the scratched surface.
For softer sanding with Super Assilex 800, 1000, 1200 and 1500 abrasives, the intermediate layer must be replaced with a soft one 9710091. The intermediate layer has a micro-zip on it, which attaches and holds the abrasive to the intermediate layer. Again, don't forget to wipe the abrasive and the surface, check the surface under the light for potential scratches and the uniformity of the sanded surface.
Sanding must be continued for a high gloss epoxy. Again the interlayer is changed, this time to the super soft velor Buflex Dry 9710065 with micro-zip and use the Kovax Buflex Dry 2000, 2500 and 3000 abrasives.
3. Machine sanding - 125 mm
We recommend starting to sand epoxy surfaces ideally 14 or more days after casting, but at least 10 days. After flattening the plane of the casting on a milling machine, CNC, in a draft or on a leveling sander, we will have a semi-finished product ready for sanding. The marks on the surface of the casting after such straightening should ideally be fine-tuned to a plane with Tri-Pro P80 sandpaper. For rough sanding of an epoxy table or serving board, a wide-belt sander (if we have access to it) or, in most cases, an eccentric sander with oscillating motion and oscillation can be used 5 mm. A five millimeter offset in conjunction with Kovax abrasive is better, faster, more efficient and with a better result than a 3 mm offset. We recommend not using a vibrating sander, which only vibrates in one direction, it clogs the abrasive a lot, it does not sand the epoxy as it should, and the choice of abrasive for this sander is also limited. We also do not recommend sanding with a drill or angle grinder, as the rotational movement results in poorer surface quality (ripples).
For efficient use of the abrasive and a perfect result when working with Kovax abrasive, we set the sanding speed on the eccentric sander to about half of the speed spectrum (mostly it is the 3rd level out of 6). This will reduce the speed, removal and heating of the material (epoxy does not like high temperatures). Above all, do not put pressure on the sander (a lot of pressure on the sander will cause scratches that will appear, for example, only after the final polishing – then it would be necessary to go back with the grain size and start the entire sanding almost from the beginning – for example, from grit 240). Hold the sander in the place where the axis passes through it – care must be taken that the sander does not lift up on one side or vice versa and thus create undulation errors by sanding. It is necessary to grind evenly over the entire surface.
Working procedure:
Start with the grit of the abrasive with which you have prepared the product – sanded (e.g.: if the product is sanded with a wide belt sander to a grain size of 120, we first sand with abrasive grit 120).
If you start sanding with Kovax Tri-Pro abrasive, sand without an intermediate layer in the order of roughness 80, 100, 120, 150, 180, 220, 240, 280, 320, 360, 400 and 500. During sanding, wipe the surface of the product and the surface of the abrasive with a cloth. Always check that the abrasive is sharp enough. Next, use Kovax Super Assilex 600, 800, 1200, 1500 abrasive with a soft Super Assilex interlayer 9710044. The interlayers are necessary so that the hooks on the sander do not break through the very elastic abrasive on the latex and then scratch the sanded surface. Again, don't forget to wipe the abrasive and the surface, check the surface under the light for potential scratches and the uniformity of the sanded surface.
Sanding must be continued for a high gloss epoxy. Again the interlayer is replaced, this time with the super soft velor Buflex Dry 9710067 with micro-zip and use the Kovax Buflex Dry 2000 and 3000 abrasive.
4. Manual polishing
We polish small things, e.g. jewelry, by hand using a small orange foam pad 80 mm, on which we apply a little Finixa polishing paste. We place the mat on the table and polish the jewelry in circular motions on it until it shines like glass. We then wipe off the excess paste and dry the jewelry with a microfibre cloth. In the case of polishing small surfaces, we proceed in the same way with the difference that we circle the entire pad with the paste over the polished surface.
5. Strojní leštění
Polishing an epoxy table and other products is a very important step, where the quality of the previous sanding is recognized. For polishing, it is advisable to use a rotary polisher with a polishing disc. An eccentric sander is unsuitable for polishing – the sander does not polish. If neccessary, you can also use a drill with a polishing attachment, but the work is much more demanding, it is not the best to manipulate, and it also reacts more poorly with pressure and revolutions, so we do not recommend this emergency procedure. It can spoil all our efforts so far. If you don't have a polisher, it's better to borrow one somewhere.
For polishing, we recommend Finixa polishing paste, which is a one-step nanotechnology-modified paste that achieves a high gloss of 95 %. Another great advantage of this paste is that it stays moist for a long time and reduces the risk of dry powder residues that can scratch the work. We apply the Finixa paste to an orange POP 714 polishing pad with a diameter of 145 mm with a set speed of 700 RPM, a maximum of 1000 RPM, and rub it over the polished surface. A short-hair polishing pad appears to be an even more suitable polishing pad. At lower speeds (up to 700 RPM), we also control the temperature of the surface beautifully and prevent possible local softening. We press only slightly and proceed with a slow and even movement over the entire surface of the table. Definitely do not stop in place (there is a risk of overheating of the epoxy, which will result in an uneven surface). At the end of polishing, clean the surface with a microfiber cloth.